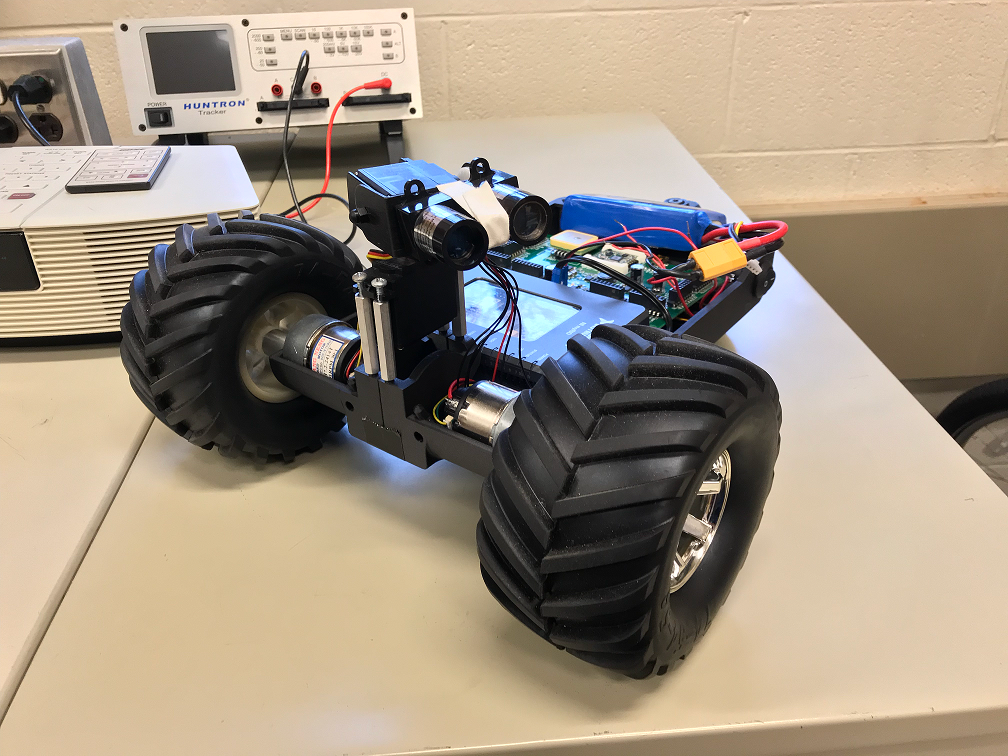
It is no secret that the engineers at Grove City are incredibly talented and innovative. One project that stood out to Dr. Mohr, an engineering professor here, was designed and built by sophomore Theo Stangebye. Instead of reading me go on and on about the complexities, Dr. Mohr thought it best Theo explain the process himself. Theo and his sister, Sophie, were even kind enough to put together a short video showcasing the technology – enjoy!
Hi, my name is Theo Stangebye and I’m a sophomore electrical/computer engineering major at Grove City College. This past semester, I’ve had the privilege of working in the control systems lab with Dr. Mohr through the independent study program. During that time, we’ve been working on developing a robot with the ability to track ants and other small insects as they move across a field in order to study their behavioral patterns.
The development of this robot has been a collaborative effort: the project was suggested by professors in the Biology department, the chassis was designed and 3D printed by a mechanical engineering student, and the robot’s motherboard was designed by Dr. Mohr.
The robot utilizes a tail-dragger design and measures about one foot in length from front to back. We’ve equipped the robot with many instruments and sensors which will eventually help it navigate in the wild, including a movable lidar sensor, an inertial measurement unit, quadrature encoded wheel, and a GPS receiver. Currently, however, the robots computes distance and direction solely based on the movement of its two front wheels. The whole system is controlled with a myRIO by National Instruments and is programmed by LabVIEW.
Working on the project this semester has been a blast. I’ve developed low level control algorithms which allow the robot to be controlled with series of simple, high level commands, such as “drive 30 inches at an angle of 45 degrees.” To enable this form of control, I utilized a PID loop, which constantly checks the direct the wheels to correct for errors in the robot’s heading. PID loops are standard in industry applications, so getting to write my own algorithm was an excellent learning experience.
There were challenges along the way, but getting to see the finished product has been very rewarding. The robot can perform complex maneuvers, like tracing a star pattern, with great amounts of precision. If you’d like to see the robot in action, please check out the video on this page. I’m excited to see we will accomplish in the future, especially as we interface cameras into the robot next semester.