Every year, the Grove City College mechanical engineering seniors work on a year-long design project to demonstrate and use the engineering knowledge they gained over the past four years. There are typically five distinct projects, each with a team of approximately eight students. Students spend the first semester designing the project and the second semester building or refining their designs. Each team is supervised and guided by an adviser throughout the design and development of the project. At the end of the year, each team presents their final design to professors, family members and project sponsors.
Because mechanical engineering is very diverse and has many different applications, every year the projects are all very different. Each project highlights a different aspect of engineering, so that each student can find a project that matches their interests. The projects for the 2015-2016 school year are described below. Check out Grove City College’s mechanical engineering website to learn more about past senior design projects.
BPMI – Control Valve Optimization
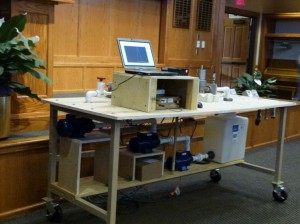
Grove City College has a long-standing relationship with Bechtel Plant Machinery, Inc. (BPMI). BPMI is a company near Pittsburgh, Pa. that contracts with the United States’ Nuclear Navy program. For the past several years, BPMI has sponsored a senior design project, typically in the area of fluid mechanics.
This year, BPMI asked the design team to optimize a control valve and provided very detailed project specifications. For this project, the team utilized 3-D modeling software and CDF software, a program that analyzes and calculates fluid flow. They also built a testing station to successfully meet BPMI’s project specifications.
Wendell August Forge – Automated Ribbon Tying Machine
Wendell August Forge is America’s oldest and largest forge that makes hand-crafted Christmas ornaments, among many other products. To replace a tedious and complicated process, Wendell August Forge asked the design team to create a machine that would automatically load and index the ornaments, while automatically tying a knot and attaching the ribbon to the ornament.
The scope of this project was very large and required a 10-person team, the largest group so far. Using 3-D modeling software and extensive mechanical prototype testing, the team was able to successfully design a machine that met Wendell August Forge’s requirements. This project required more hands-on work to build and test the machine that some of the other projects.
HVAC Missions Project – Christian Leadership University in Burundi, Africa
HVAC stands for Heating, Ventilation and Air Conditioning, and is a subset of mechanical engineering that deals primarily with thermodynamics, fluid flow and heat transfer. Almost every year, there is an HVAC-related senior design project. This year, the HVAC team worked to create the building plans for the Christian Leadership University building that may one day be built in Burundi, Africa. This project had a missions-based component because the team worked with contact Len Rosenberg and Ministry Architecture, Inc. Ministry Architecture, Inc. works to design buildings for ministry organizations throughout the world with the goal of advancing the Gospel.
This project is different from other projects because the team’s only deliverable was a set of HVAC design plans based on Len Rosenberg’s architectural designs. They did not have to physically build a machine or system. This project required HVAC knowledge, as well as the use of a program called Revit to create a 3-D model of the proposed building.
United Plate Glass – Automatic Kevlar Rope Winder
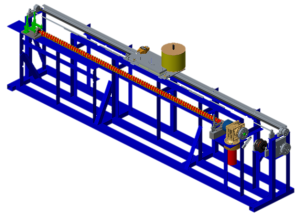
United Plate Glass (UPG) is a local company that specializes in tempered plate glass products. Part of its manufacturing process involves large rollers wrapped with Kevlar rope to prevent the glass from breaking. UPG asked the design team to create a machine that would automatically and uniformly wrap Kevlar rope around the rollers so the UPG workers no longer had to do this. Because the team’s final design is to be installed in UPG’s factory, the machine had to be production quality.
To complete this project, the team relied on 3-D modeling software, Finite Element Analysis (FEA), and machine design knowledge. Because the machine was to be installed in UPG’s factory, safety and reliability were stressed. The team was able to successfully design and build a machine that met all of UPG’s requirements.
AntBot – Ant Tracking Robot
For the past year or so, the Grove City College biology department has been tracking and studying the behavior of ants. Engineering students have even written computer code to filter and track ants’ motions. For this project, a team of both mechanical and electrical engineering students was formed to design a robot that would automatically track ants.
This project required significant knowledge of control systems and image processing because the robot had to identify the ant’s location, as well as follow it to its next position. The compute code written by engineering students in the past was improved and enhanced to better track the ant. This project required a close relationship with the electrical engineering team to successfully develop and test the robot.